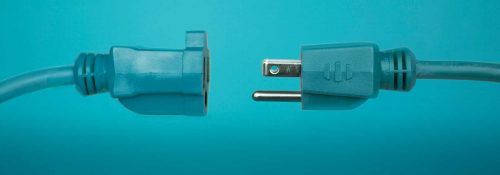
Think Bigger: Hidden Costs of Design Decisions
![]() |
GSA’s U.S. Custom House, Baltimore, MD |
Steven Forrester’s small Colorado engineering firm is four years old. While he started DMA Engineering during tough economic times, he is holding his own because of clients like the city of Louisville, where his firm recently designed a solar thermal lap pool for a city recreation center.
In a competitive environment where many small firms have closed their doors, one of the ways DMA sets itself apart from other firms, large and small, is by incorporating life cycle cost analysis, or LCCA, into nearly all projects at no cost to the client.
“When we present a design, 99% of the time, we do LCCA, “ says Forrester. “It shows we bring added value.”
In the case of the solar-heated pool, the facilities manager had to go to City Council members for approval. The LCCA demonstrated the financial incentive to do the project. Forrester uses LCCA mainly to compare different types of systems over the lifetime of the building. The price of new equipment is an easily comprehensible but incomplete cost. LCCA also accounts for future costs. LCCA adds in maintenance, energy use, tax incentives or rebates, and any salvage value. It also can cover replacement costs. For example, really good windows may last 50 or more years, so it’s not likely building owners would account for their replacement. Rooftop units, on the other hand, which are usually considered an inexpensive heating and cooling solution for commercial buildings, must be replaced much more frequently. “We typically see replacement 10-25 years,” says Forrester.
That means if design teams are thinking about the lifetime of the building, then the cost of one rooftop unit is really the cost of three, six, or nine units or more, explains Rocky Mountain Institute Analyst Roy Torbert. RMI recommends LCCA as standard practice on all new and retrofit building projects.
“Most equipment will be around for 20 years. Without doing the lifecycle analysis, you only know the initial costs rather than the full cost over the life of the building,” says Forrester. “I think it’s an invaluable part of making any decision about any piece of equipment.”
While Forrester compares the direct economic costs of alternative design solutions, some people and organizations are beginning to consider the indirect, more complex societal costs.
Burning coal emits sulfur and nitrogen oxides (causing acid rain), particulates, mercury and other toxic metals. Coal ash from power plants pollutes streams. Mining coal injures and kills workers and inverts landscapes. Such hidden costs of U.S. coal-fired electricity total $180 billion to $530 billion per year, according to RMI research.
“The price of coal-fired electricity—which is over half all the electricity in the U.S.— would double or triple if we accounted for its hidden cost. It’s important that we begin to think in a little bit larger picture when it comes to making design and business decisions, and we are beginning to see the change,” says Rocky Mountain Institute Consultant Mike Bendewald. Bendewald is managing an RMI project to help the U.S. General Services Administration (GSA) Mid-Atlantic Region account for hidden, societal costs when making commercial building retrofit decisions. Working with Steven Winter Associates and the Athena Institute, RMI is helping GSA to use life cycle assessment to account for the environmental impact of building retrofits and operation, and will then convert the impact into a dollar value.
Life cycle assessment, or LCA, estimates the environment impact of processes and products in terms of greenhouse gas emissions, wastes, toxins, and particulate matter. GSA will wrap the hidden costs associated with this impact into the LCCA in order to provide a fuller analysis.
Design teams can use LCCA to show the tradeoffs between cost and another factor that is important to the client, such as carbon. Since President Obama has ordered all new federal buildings to be net zero by 2030, many energy service companies working on federal projects will be closely examining these kinds of tradeoffs. Boulder Green Building Guild recently asked Bendewald and Torbert to present on LCCA and LCA to its members, who, like Forester, are increasingly interested in offering this kind of analysis to clients.
To encourage wider use of LCCA, Forrester believes we should make LCCA a formal part of the construction process, such as a stamp drawing, certified to a standard. “If LCCA had a leg to stand on, you could take it to a bank or an appraiser and say the one with the more efficient system is the more valuable building.
“We really need to get the financial planners involved and make the tools more streamlined in order to make LCCA more mainstream,” says Forrester. Then, perhaps he wouldn’t have to offer it for free.