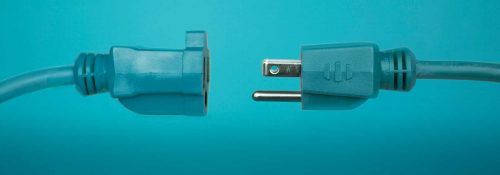
For As Long As The Sun Shines: The Non-Crisis of PV Module Reliability
What’s included in every Yugo owner’s manual? A bus schedule. This is just one of countless jokes about the car that some have called the worst in history and that TIME magazine named to its list of “50 worst cars of all time.”
Many people realize that buying the cheapest car or appliance on the market might mean purchasing another in a couple of years when it breaks down. The old adage “you get what you pay for” is never truer than when it comes to important appliances. So it shouldn’t come as a surprise that with the rise of the PV industry, companies are competing to come out with more affordable solar panels that aren’t quite making the grade.
A recent article in the New York Times, widely reprinted in other news outlets, reported the solar industry is facing a quality crisis as photovoltaic panels are failing at an alarming rate. This type of press can do a lot of damage to the maturing and growing solar industry. Yet, how prevalent is this so-called crisis, and is it grounded in fact?
Like a rock
Historically, PV modules have been extremely reliable. The first solar modules became available for residential applications in the 1970s. There were a handful of companies manufacturing those pricy panels, and many of those panels are still producing electricity today. Martin Holladay, of the Green Building Advisory Council, recently took his 1979 Arco Solar PV module off his roof to test it. It performed better than the factory specs. “My old module shows no signs of browning, electrical corrosion, or water intrusion,” said Holladay in a blog post. “It certainly looks as if it’s ready to perform for another decade or two.”
Since PV modules have no moving parts they seem like pretty simple products. However, a module comprises dozens of materials and components—back contact sheets, semiconductors, transparent conductors, encapsulates/sealants, solder joints, glass, and bypass diodes. Although the technology itself is extremely reliable, each of these components has various and sometimes independent failure mechanisms that could lead to poor module reliability. Nevertheless, historic module reliability studies show the risk of failure is relatively low.
“A PV cell is a rock that makes electricity,” PV dealer Joel Davidson told Holladay. “Unless something corrodes the electrical contacts, it will still keep working.”
Yet in the past few years some newer modules have been underperforming at a higher rate. The rising demand for solar panels has led to increasing competition and falling prices as the market matures and modules inch closer to commodity status. As examples such as the Yugo have shown, though, prices can only go so low before corners are cut on quality. Like any product, lack of quality produces a substandard product.
Quality control
As with any industry, solar panels need quality control. This is where the International Electrotechnical Commission (IEC) comes in. The IEC sets standards for all electrical and electronic technologies. IEC Technical Committee TC82 was established in 1981. It is the most important International body regarding photovoltaic-related standardization. The main tasks of TC82 are to prepare international standards for photovoltaic systems. Underwriters Laboratories (UL), which develops safety standards for electrical devices, is helping to develop global IEC standards, and is a leading organization in the global efforts to harmonize the UL and IEC PV standards with industry.
Certifying bodies around the world perform PV module testing to IEC standards. Modules that are qualified to IEC standards are much more likely to survive in the field and not have design flaws leading to premature failure, or “infant mortality,” as it is known in the industry. An NREL study, reporting on ten years of field results, showed that unqualified modules suffered from 45 percent field failure rates while qualified modules suffered from a less than 0.1 percent field failure rate.
“There is a wide spectrum of sophistication, quality, and performance when it comes to technology products,” Jenya Meydbray, CEO of technical solar due diligence firm PV Evolution Labs, wrote in Renewable Energy World, “from cameras to computers, from mobile phones to motorcycles.” Solar panels are no different. Based on the hundreds of solar panels that have gone through rigorous reliability testing in the PV Evolution laboratory, the vast majority of modules have proven to perform very well.
Solar’s undeserved reliability reputation
So what is all the negative hype about? Much of the bad news of PV modules is being blamed on Chinese manufacturers. Yet not all Chinese manufacturers are producing problematic panels. China’s largest PV manufacturer, Yingli Solar, has its panels independently tested by TÜV Rheinland, one of the largest PV-certifying bodies. To maintain existing “Power Controlled” certificates, TÜV Rheinland will randomly select samples from production lines and warehouses for verification testing throughout the year. Yingli asserts only 15 defective panels were returned out of the 2.8 million shipped to the U.S. since 2009.
Another example used in the Times article to illustrate the supposed crisis facing the PV industry is based on one of the United States’ largest manufacturers, thin film company First Solar. In late 2012, the company resolved to replace 232,000 modules manufactured in 2008 and 2009 that might develop a loose cord plate attachment. First Solar worked with system owners to repair and replace all of the potentially defective modules which represented a very small fraction (about two percent) of the almost 2.2 GW of modules they produced during the same time period. Though First Solar’s stock prices took a temporary hit, currently investors are rallying behind the company, with Q1 2013 revenue higher than expected.
Besides overstating the failures in the PV industry, the Times article also misrepresented data. The author claimed testing of six manufacturers’ solar panels at two Spanish power plants by Enertis Solar in 2010 found defect rates as high as 34.5 percent. This is true, but testing actually showed a range between 3.1 percent and 34.5 percent. And the modules didn’t fail completely. They were still functional, and rather had thermographic defects. A thermographic defect means that when examined with an infrared camera the modules showed hot spots. The modules with the hot spots tended to lose output faster than other brands, but even then by less than a percentage point. This is not a failure of a PV module—all PV modules lose max power output over time, on the average losing less than 0.5 percent per year.
Stamps of approval
Every company and industry experiences quality problems. That’s why people research products before they buy them. In solar, this means people are realizing they may have to pay a bit more upfront (in $/W) for quality to pay less for what they actually care about: long-term performance (in cents/kWh).
Unfortunately, there is no Consumer Reports for solar panels. There has been a three-tier rating system for module manufacturers, though recently the rating system’s value has been called into question.
PV Evolution Labs and GTM Research hope to resolve such quality assurance issues and allay concerns of potential consumers by providing reliable information about, well, reliability. The two have developed a Research PV Module Reliability Scorecard, which relies on testing and evaluation to help PV manufacturers prove the performance of their production modules. It also allows project developers, installers, and investors to better understand how the modules will perform over their anticipated lifetime. The scorecard is based on results from PV Evolution Lab’s Reliability Demonstration Test protocol and GTM Research’s cost and bankability analysis.
The reliability issue is also at the heart of financing and renewables investment. Just as lenders in part use a consumer’s FICO credit score to evaluate risk in assigning a mortgage, solar investors are seeking ways to better gauge risk in projects. RMI is involved in efforts to solve that through truSolar, an industry working group developing uniform open-source risk scoring standards and rating criteria for commercial and industrial solar projects. NREL’s Solar Access to Public Capital (“SAPC”) working group, which works on standardizing a number of project financing elements as well as providing data that can help assess PV project performance, aims at similar goals.
Don’t let the sun go down on solar
As with any industry, quality control for PV modules is important. All PV modules are not created equal, and we need better tools and honest data to identify high-quality manufacturers and move the entire PV industry toward greater quality standards, while not letting a few bad apples spoil the whole bunch.
More than 16 million cars were recalled last year, yet nobody is heard crying the auto industry is in a crisis. So it should be with solar. “A few quality issues in a nascent industry that’s growing at double digit rates,” argues Meydbray in Renewable Energy World, “does not represent the broader technology.”
Solar panels might not be quite as reliable as the sun itself, but they’re improving every day as the module manufacturing industry matures, with reliability rates that are already pretty bright.
Image 1 courtesy of shutterstock.com. Image 2 courtesy of shutterstock.com. Image 3 courtesy of shutterstock.com.