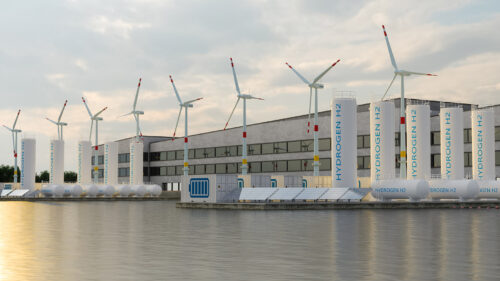
Hydrogen Reality Check: Distilling Green Hydrogen’s Water Consumption
Water access and requirements for green hydrogen production can be effectively managed if intentional sourcing, project siting, and efficient use is prioritized.
The Myth: Scaling green hydrogen will severely impact global freshwater supply because it uses far more water than other hydrogen or equivalent energy production processes.
The Reality: The additional draw on the world’s water supply from producing the green hydrogen needed for a 1.5°C-aligned future will be minimal. To produce the same amount of energy, green hydrogen often consumes less water than fossil fuel-based hydrogen or some types of electricity generation. However, this does not negate the imperative that green hydrogen developers prioritize efficient process design and consider local water availability in project planning. In areas of water scarcity, consideration of alternative sources such as treated wastewater or desalinated sea water can minimize freshwater reliance.
Scaling up clean energy technologies without infringing on water access is essential in ensuring real and lasting solutions to the climate crisis. Green hydrogen has made a splash for its role in addressing the 30 percent of global emissions from industries that have no alternatives for decarbonization, making it essential to consider this technology’s impacts on water supply.
Distilling Green Hydrogen’s Water Consumption Down to the Kilogram
Green hydrogen, made by separating the H2 from H2O with renewables-powered electricity in a unit called an electrolyzer, consumes a similar amount of water to other processes used to produce hydrogen. All methods of producing hydrogen require water, and green hydrogen does not consume a significantly greater amount than its alternatives.
Per chemistry fundamentals, 9 liters (L) of water are required to produce 1 kilogram (kg) of hydrogen via electrolysis. When layering in the additional volume required for water purification and process cooling, an additional ~10-20 L/kg is needed. Inefficient designs such as evaporative cooling systems may exceed this range, but those systems are uncommon, especially at large scales of production. Green hydrogen’s cumulative 20-30 L/kg of water consumption is on par with or even less than the 20 to 40 L/kg of water required for fossil-based hydrogen production pathways, as seen in Exhibit 1.
Zooming out beyond the bounds of the hydrogen production plant, the source of electricity and/or natural gas could add “embodied” water consumption to all hydrogen pathways. Electricity generation- for use to power the fossil-based hydrogen plant or split water via electrolysis can have a range of water requirements depending on the source. Green hydrogen’s reliance on renewables minimizes additional water consumption.
Fossil fuel power generation requires a substantial amount of water for temperature regulation, and as such, electricity drawing from the grid which includes sources like coal or gas will see a greater amount of water consumption than electricity largely sourced from solar or wind. Gray and blue hydrogen will have significant upstream water consumption from natural gas drilling, extraction, and processing, which collectively could add over 5 L/kg hydrogen, depending on how and where the gas is extracted. In contrast, green hydrogen systems do not rely on such feedstocks and heightened plant standardization will limit additional water consumption.
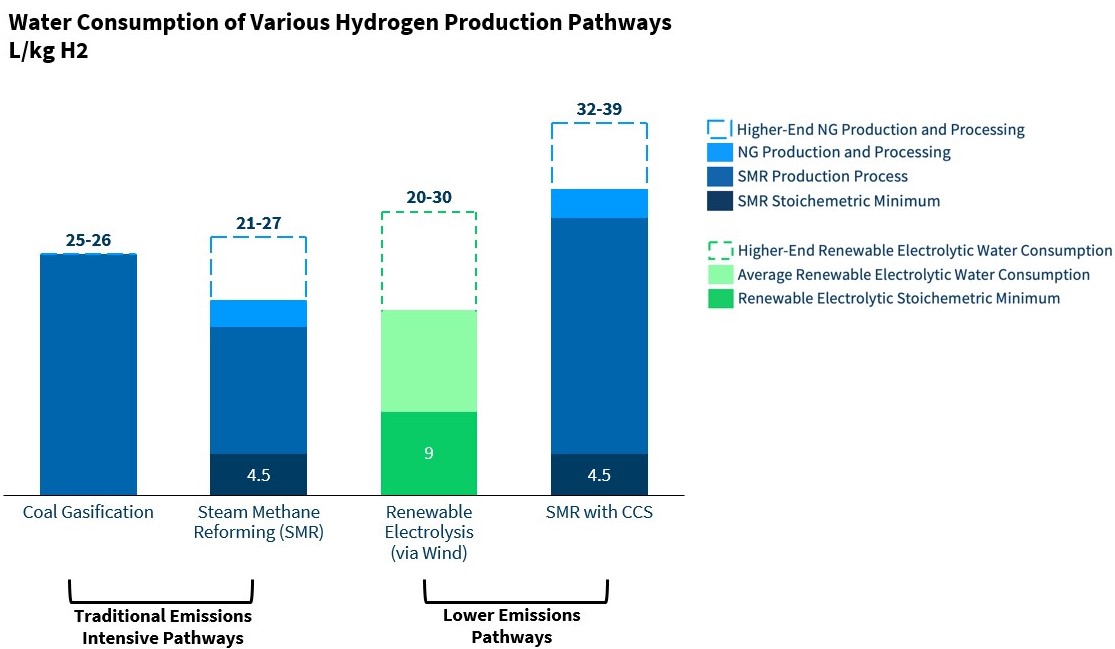
Put in context with other large-scale water consuming processes used today, to produce the same amount of energy green hydrogen production consumes less than half the water of typical coal or nuclear electricity production.
Additionally, there is an inherent circularity in the process of producing and consuming green hydrogen. Some end-uses of hydrogen could be designed with these circularity principles in mind to minimize water consumption. For example, when hydrogen is used for steelmaking, it is converted to water; this water can be captured and fed back to the electrolyzer to produce hydrogen again.
Often A Drop in the Bucket
Producing the amount of hydrogen that the energy transition needs will require a lot of water, but in the context of how much water we already use, the amount will be insubstantial. Let’s dive in.
The world uses 4 trillion cubic meters of freshwater per year and the United States is responsible for 338.5 billion cubic meters of that. As seen in Exhibit 2, most of that water goes towards irrigation and thermoelectric power, while all the showers, dishes and other personal uses only make up 14 percent of total US usage.
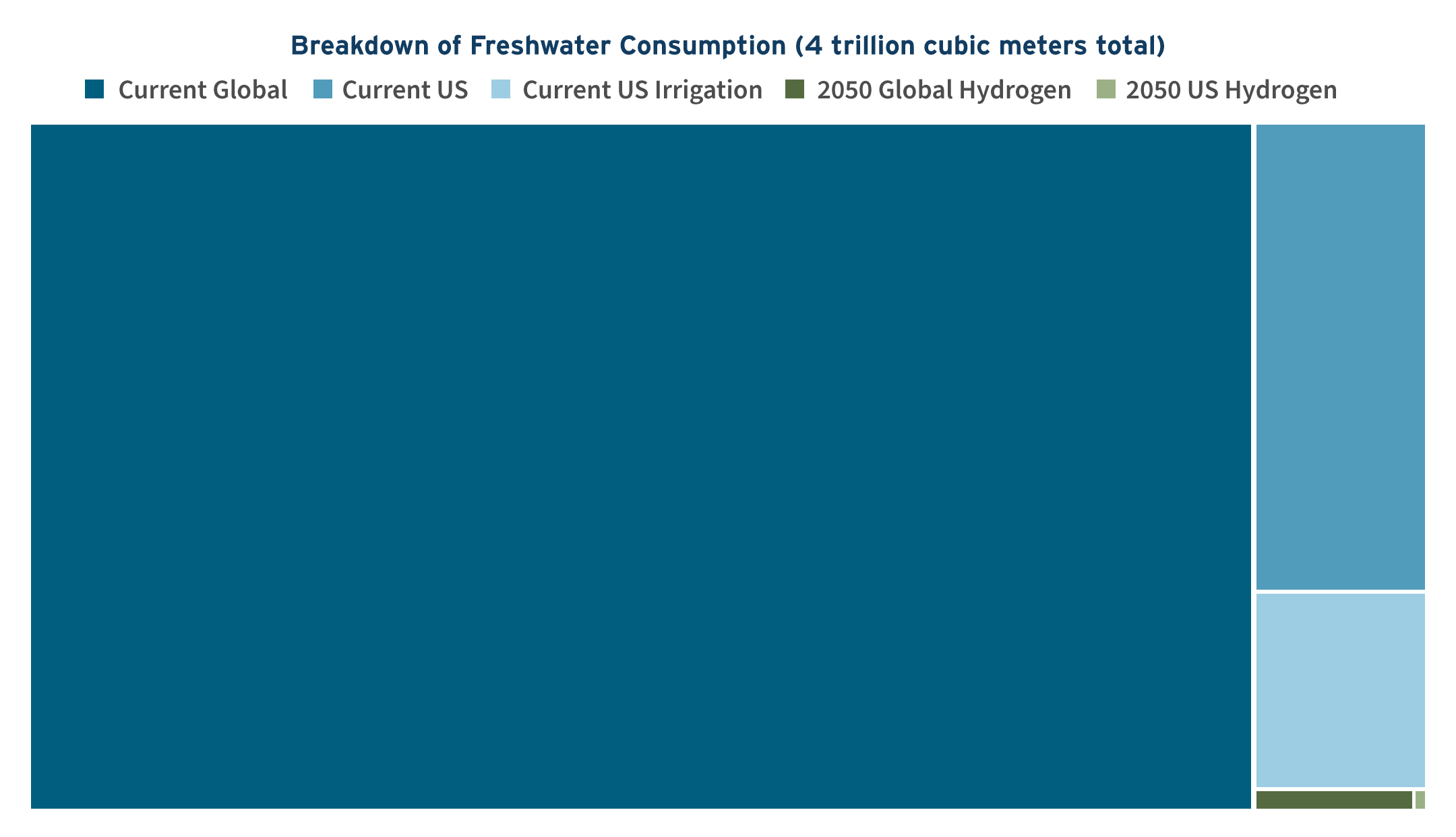
Come 2050, projections estimate that hydrogen will have a relatively small draw on global water usage. The DOE National Clean Hydrogen Roadmap targets 50 million metric tons (MMT) of clean hydrogen annually produced by 2050. Assuming all this hydrogen is produced via electrolysis at 20 L/kg, this would require 1 billion cubic meters of water, or 0.26 percent of US current water usage. Globally, estimates for future hydrogen demand vary widely, but using the Hydrogen Council’s forecasted 660 MMT of demand would require 13.2 billion cubic meters of water, or 0.33 percent of current global freshwater. This analysis doesn’t consider potential water savings from hydrogen replacing water-intensive industrial processes.
What does a kilogram of hydrogen actually mean for such savings? The amount of water an average bathtub holds in the U.S. (~300 L) could be used to create green hydrogen and drive a hydrogen fuel cell truck over 235 kilometers. On the other hand, with that same bathtub’s water, a diesel-powered truck would only make it 141 km due to diesel’s inefficiency and higher water footprint.
Water availability is a local issue, and much of the world is facing general water stress or severe drought in part due to climate change. To understand how hydrogen production will impact a water-constrained US state, let’s look at Utah. Utah is in the process of developing the Advanced Clean Energy Storage (ACES) project, one of the largest proposed green hydrogen projects in the United States with 220 megawatts of electrolyzers. ACES will produce 100 tons per day of clean hydrogen, requiring 730,000 cubic meters of water per year, or 0.012 percent of Utah’s current yearly water usage (by comparison, Utah uses approximately 40 times as much water irrigating its golf courses).
Turning down the Tap
Although green hydrogen will not significantly add to global water consumption, diversification of raw water sources, careful consideration of project siting, and review of water pricing schemes will help limit strain on local freshwater access.
Green hydrogen requires highly purified water as a feedstock, but that water does not need to come from freshwater sources. There are proven technologies that can be used to bring seawater, industrial wastewater, municipal wastewater, or water within food waste to a purity that can pair with green hydrogen water polishing systems to achieve the required 99.9 percent purity levels. These technologies are commercially mature and used at scale in other industries today. Inclusion of such technologies can come at low additional cost and energy requirement to the system — often adding no more than $0.10/kg to the levelized cost of hydrogen (which in total is on average between $2 to $5/kg) and using 1 percent of the electricity required for electrolysis itself. In coastal communities with large populations, there could be an opportunity to upsize desalination plants to provide additional clean water benefits to these communities.
Intentional siting of green hydrogen projects is a proactive measure to avoid adding strain on water systems, and permitting processes should include assessment of local (and downstream) water availability, competing uses, and rights. This will ensure that projects are not committed to in locations that cannot support its water needs and are built in accordance with local water policy. Synergies could be seen in pairing new build green hydrogen plants in locations of retired coal plants or water-intensive industries, providing continuity of water allocation at a local level.
Reviewing and revising the pricing schemes of water may be required to better align the scarcity of this essential resource with the economic value placed upon it. Water rate structures are typically either uniform or block based. In a decreasing-block structure, as users consume more water, they are given a discount at each marginal block as a “bulk” discount. Considering water pricing structures that place a higher cost of water for bulk industrial users, such as increasing block rates, could incentivize users to build green hydrogen production systems that prioritize design efficiency and the use of non-freshwater feedstock to limit freshwater water consumption.
Regional water availability must be considered in project planning, and the tactics outlined for project siting, system design, and water sourcing can help limit green hydrogen’s water impact on a local level.