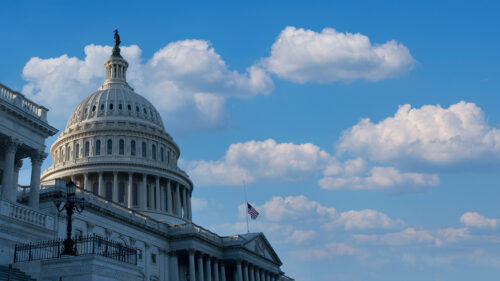
How Policy Can Advance a Circular Battery Economy
Five critical elements that can help mitigate the risks associated with battery production while strengthening the EV battery supply chain
As we note in our overview of the electric vehicle battery supply chain, the way we produce EV batteries today can be associated with human rights abuses and environmental degradation, vulnerable to disruption, and unable to meet growing EV demand.
A circular battery economy, one in which used batteries are repurposed or recycled, can help mitigate the risks associated with battery production while at the same time strengthening the EV battery supply chain. By repurposing and recycling EV batteries, we can decrease our reliance on virgin materials and negative community impacts associated with their extraction. We will also reduce the risk of supply chain interruptions due to changing trade alliances, geopolitics, and extreme weather.
To make a circular battery economy a reality, we will need robust policy that:
- Provides a standard federal compliance approach and works to harmonize against global battery supply chain rules and regulations;
- Clearly describes how businesses can increase supply chain traceability, material transport and storage, manufacturing and production, recycling, and repurposing; and
- Details how businesses can track compliance.
This article outlines the types of policies that can form the basis for a circular EV battery supply chain and delineates the tradeoffs inherent in designing specific circularity policies.
The Importance of Policy
The economic viability of battery reuse and recycling is currently challenging, given economic uncertainties. Today, it’s often cheaper to mine for minerals or produce new batteries using the status quo for linear processes. The economics of recycling vary greatly based on the material composition of the battery and the related market value of constituent minerals. If it takes place at all, most recycling seeks to recover higher value nickel, cobalt, and lithium.
By enacting battery circularity frameworks, recycling and repurposing used EV batteries can become self-sustaining or even profitable. Without effective battery circularity polices, this market could go the way of plastic recycling, which, in the United States, is currently at 8 percent. The dismal rate of plastic recycling is mostly due to a lack of adequate regulatory frameworks and the fact that it’s cheaper to create new plastics than to recycle used plastics. If policies discouraging single-use plastic and extending producer responsibility had been in place when recycling was in its early stages, recycling rates would most likely be higher.
Given the urgency of the climate crisis, and the significant investment required to create a circular battery economy, policies can serve as a powerful market signal to demonstrate government priorities and help catalyze much needed investment.
What Would Effective Policy Look Like?
Effective policies will not be written overnight, especially considering the global nature of the EV battery supply chain. To avoid wasting time, money, and other resources, local, national, and international policies will need to align with global battery circularity best practices.
Today, the US has no federal recycling mandates or requirements for lithium-ion batteries, and state policies differ significantly; the lack of uniform standards translates to a piecemeal, insufficient approach to battery circularity. Clear federal guidelines would greatly expedite the creation of a robust and circular battery economy.
It’s also important to note that no policy will be perfect: every approach has its benefits and challenges. The private and public sectors must collaborate intensely so that policies meaningfully advance a circular battery economy.
Below we describe five policy features that can be applied globally to ensure effective policy implementation, including current legislative and voluntary examples as well as key considerations.
1. Supply chain traceability
Today’s EV battery supply chain is opaque, making it difficult for midstream and downstream actors to determine where their raw materials come from. This opacity means it’s hard or even impossible to know if the materials were extracted using child or forced labor and how mining affects local environments. By making the supply chain more transparent and/or traceable, industry actors and policymakers can better address the abuses associated with mining. Transparency can also help the public and private sectors know where batteries are and the quantity of materials available that could be recycled or repurposed.
The European Union has taken a significant step to improve supply chain traceability by adopting a battery regulation that requires recycling an increasing percentage of a battery’s weight. Manufacturers now have to disclose a battery’s carbon footprint and recycled content, and whether its materials come from mines that engage in human rights abuses. Upstream actors are required to undergo third-party audits of their mines to ensure that materials are being ethically extracted. The EU Parliament recently approved a directive that requires that companies based in the EU identify, prevent, end, and/or mitigate the negative impact of their activities on human rights and the environment.
Battery passports, which digitally track a battery’s production and use throughout its life cycle, are also a powerful tool that improves transparency. The Global Battery Alliance, a public-private consortium that includes original equipment and battery manufacturers, created the battery passport framework, which the private sector is beginning to adopt.
Improving traceability is no small feat; it will require private and public stakeholders to gather, store, and organize large amounts of data. Further complicating matters is the fact that there is no agreed-upon standard practice. However, traceability is essential and represents a cross-cutting policy feature. Without a framework to measure and manage the supply chain flow of these materials, all those involved in the EV battery supply chain cannot effectively reuse or recycle batteries.
2. Material transport and storage
Today, regulators treat used batteries as hazardous materials and hazardous waste regardless of a battery’s state of health (SOH), which measures how a used battery compares to a new one and is not easy to determine. Batteries’ classification as hazardous adds delays and costs to the battery reuse and recycling process. It also means that used batteries must be transported and stored in the same way as new batteries. Currently, battery storage and transport account for 40–60 percent of battery recycling costs, which is why the private sector is hesitant to invest in recycling facilities and processes, as there can be little financial incentive to do so.
One way to incorporate more nuance into existing battery transport and storage practices is through transparent labeling of batteries. By revisiting these waste classifications and using battery diagnostics to provide clearer and more nuanced waste management distinctions, companies can transport and store batteries based on a battery’s specific risk profile instead of using an expensive one-size-fits-all process.
Reducing the regulatory burden for batteries with remaining capacity will make it easier to seamlessly integrate battery reuse and recycling into the battery supply chain. Clearly listing SOH, remaining capacity, and chemistry on a battery can help regulators create more meticulous waste distinctions and remove the regulatory barriers for “healthier” batteries. Easy-to-access information on the battery’s SOH can signify to market actors the level of degradation and remaining capacity, enabling stakeholders to identify the most viable secondary use.
3. Manufacturing and production
Currently, there is no requirement to design batteries with the primary intention of being easily recyclable, which means that every kind of battery must be disassembled in a specific way, making it difficult to scale battery recycling and repurposing. Also, the cost of extracting critical minerals from batteries after initial use is often higher than simply producing a new battery, discouraging recycling and reuse.
Effective policies will involve policymakers and businesses working together to determine how battery circularity can be profitable for any EV battery, regardless of vehicle assembly or battery chemistry. Standards requiring that batteries and EVs be manufactured in ways that make EV batteries easy to recycle and repurpose can encourage the implementation of these practices and ensure the costs of doing so are not passed on to consumers and insurers.
Although the Inflation Reduction Act, the US climate bill passed in 2022, does not include provisions that directly address battery circularity, it does require a specific percentage of battery materials to come from North America or countries with which the United States has a free-trade agreement (FTA). This stipulation has the potential to encourage more investment in recycling and repurposing facilities. Because it will likely take years to set up operational mines and processing facilities in North American and FTA countries, manufacturers are increasingly interested in exploring recycling and repurposing used batteries to help them meet the growing demand for EV batteries.
4. Recycling
Recycling — the extraction and reuse of battery materials in another product, including another battery — has the potential to reduce the demand for raw minerals by up to 64 percent by 2050. Recycled battery scrap — the residual materials discarded during battery production — alone can serve as critical input material, reducing the need for virgin critical minerals such as cobalt and nickel.
Policies that require manufacturers to meet recycling targets, like those enacted in South Korea, have the potential to meaningfully accelerate battery recycling in the United States. South Korea’s legislation is also notable for providing dedicated funding to research and development to improve battery circularity.
The private sector is also exploring how to increase battery recycling in their business practices. For example, battery producers and original equipment manufacturers have formed joint ventures dedicating research and development funding toward battery recycling solutions: in 2021, Umicore and Volkswagen formed such a partnership, and in 2022, General Motors partnered with Lithion Recycling to develop a recycling strategy.
Simply put, effective policies should address recycled material content requirements, provide funding for research and development, and stipulate the recycling of manufacturing scrap. However, compliance with such policy frameworks will initially come with an upfront cost. Policymakers and industry leaders should work in tandem to align on what incentives are needed to help advance robust battery recycling.
5. Reusing
Battery reuse differs from recycling in that it involves upgrading a battery so it can be used again in an EV or other form of stationary energy storage. In different regions globally, we find that policies that mandate extended producer responsibility (EPR) can help increase material repurposing and reuse by requiring that manufacturers assume responsibility for a product’s end-of-life management once a consumer no longer uses it.
The Product Stewardship Institute notes that EPR policies shift financial and management responsibilities away from the public sector to manufacturers. Effective EPR policies also provide manufacturers with incentives to encourage them to incorporate environmental considerations into their products’ design and packaging, making batteries that are easier to repurpose.
While policies that include EPR promise to increase battery repurposing, consumers risk footing the bill if manufacturers pass on the cost of complying with EPR to them. Another thing to consider when integrating EPR is its possible effects on existing vehicle scrappage and salvage companies: EPR policies can disrupt this market which is why hybrid approaches may be considered, allowing salvage companies to opt-in to EV end-of-life management.
In addition to integrating EPR, effective policies will include regulations that set reuse targets, define who is responsible for ensuring that EV batteries are repurposed and eventually recycled, and impose standards on the batteries’ SOH.
We Need a Cohesive National Policy
Well-thought-out policies are required to successfully create a circular battery economy. Without policy, industry stakeholders are not likely to prioritize or invest in recycling and repurposing efforts.
A cohesive national policy agenda on battery circularity will be the most effective strategy. A piecemeal approach with redundant and contradictory policies will not suffice, given the global scale of the battery supply chain.
There is no one path to achieve a circular supply chain, but policy can and will be a driving impetus for its creation. Given the supply chain’s complexity, and the many actors involved, each policy will necessarily include tradeoffs; and businesses and policymakers will need to work together to improve traceability, reduce complexity, and provide incentives.