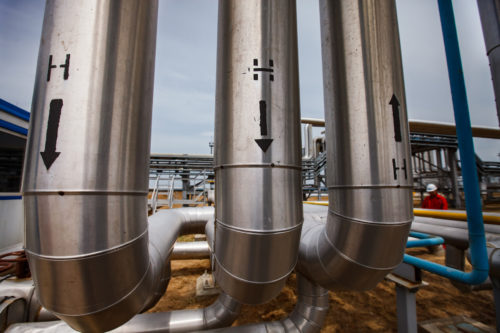
Growing Gigawatts of Green Hydrogen
A look at how we can deploy the hundreds of gigawatts of electrolyzers needed this decade
Of all the technologies unleashed in the energy transition, few have generated the level of excitement that green hydrogen has. As a potential enabler of economically viable, zero-carbon solutions for everything from steel manufacturing to marine shipping, green hydrogen is positioned as a cure-all for the “hard-to-abate” sectors. This has drawn interest from many of the world’s largest companies, with steelmakers, refineries, and fertilizer producers driving the majority of current projects.
However, there remains a wide gulf between the promise of green hydrogen and the reality on the ground today. There are 0.3 GW of electrolyzers powered by renewable energy installed today with a projected 40 GW to be commissioned by 2030 according to Bloomberg New Energy Finance’s (BNEF) Hydrogen Production Database. This project pipeline pales in comparison to the 850 GW of electrolyzers needed by 2030 for hydrogen to play its part in a net zero world.
We Must Start Now
We are face-to-face with a need and opportunity to rapidly scale green hydrogen and it is critical we start now, for several reasons. First, we risk locking ourselves into a fossil fuel-based future with a significant stranded asset risk if we do not actively pursue a zero-emissions pathway today.
Second, we could contribute to growing a mismatch between electrolyzer manufacturing capacity and the demand for electrolyzers if we do not actively develop more projects. Taking BNEF’s recent survey of available manufacturing capacity and proposed project pipeline, within the next 5 years projects could only account for 25% of available manufacturing capacity. If these assessments are true, original equipment manufacturers (OEMs) will compete over supply of proposed projects to fill order books, potentially cutting the price of electrolyzers to unsustainably low levels for increased competitiveness.
As a result, OEMs will not see significant return on investments until the overcapacity of the supply market is remedied, but instead will be forced to operate on tight or negative profit margins. Demand must increase to fill order books, which in part will be accelerated if costs fall more rapidly than expected. But regardless of the potential cost point, off-takers must recognize the need for green hydrogen today and begin to plan a future with green hydrogen in mind to ensure there is a match between supply and demand.
Finally, we will expedite the opportunity to enable dramatic cost reductions far sooner than expected and will foster green hydrogen’s widespread cost competitiveness once we start to scale, as seen in the chart below.
With a reduced electrolyzer capital cost, projects see greater flexibility in where they can be sited and how they should be designed. Locations with less abundant and more intermittent renewables will become cost-competitive producers of green hydrogen. Projects will see a different and cheaper mixture of renewables built to maximize cost savings now that cost competitive production can allow for more intermittency in electricity supply given a lifting of previous economic constraints.
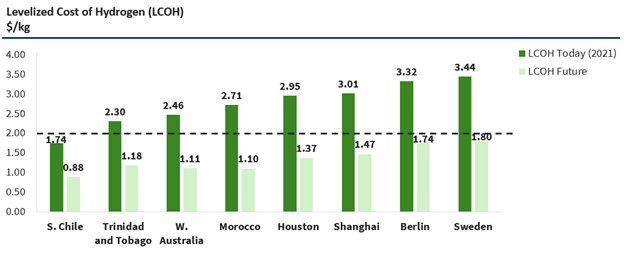
Overcoming Capital Challenges
However, although these risks of delaying green hydrogen deployment and opportunities for low-cost production are clear, scaling green hydrogen is challenging. This is especially true given limited public policy support and a narrow set of criteria that must be met for project viability. Driven by high electrolyzer capital costs, projects today require a significant amount of upfront capital to be paid out. As a result, high and early cash flows must be prioritized, driving a need to operate the electrolyzers as many hours of the year as possible.
Viable green hydrogen projects are therefore restricted to locations with ample and steady supplies of renewable electricity to maximize the resulting hydrogen production. Additionally, electrolysis plants often must be collocated with points of demand off-take as high storage and transportation costs add to the already high cost per kilogram, sending costs above the upper bound for parity. These two criteria, quality renewables and collocation with off-take, greatly limit the breadth of feasible projects, as it is rare that locations of demand are located alongside optimal renewable availability.
Even with these constraints, there are several strategies that can create favorable economics to support getting projects off the ground today. These tactics utilize the current technological standards of the system but modify project design, operation, or off-take strategies to enable cost reduction. Three of these methods include producing hydrogen exclusively during times when the sun is shining or the wind is blowing, integrating green hydrogen into existing grey hydrogen supply, and supplementing the system’s electricity input with curtailed power to reduce costs.
Matching Hydrogen Production with Renewable Output
Conventionally, we think of supplying a constant stream of hydrogen for every hour of the year. This imposed constraint drives up the amount of storage required to smooth out any intermittencies in production due to the natural variability of renewable electricity and requires an oversizing of renewables to create a stock and flow of hydrogen.
The desire for around-the-clock hydrogen production is not without warrant: ammonia synthesis and steel manufacturing traditionally require a steady stream input to avoid ramping up and down equipment. However, where off-takers can absorb intermittent hydrogen production, namely one that follows the natural availability of renewables throughout the year, projects can immediately unlock cost savings of $0.60/kg to $1.20/kg. This is seen in the chart below.
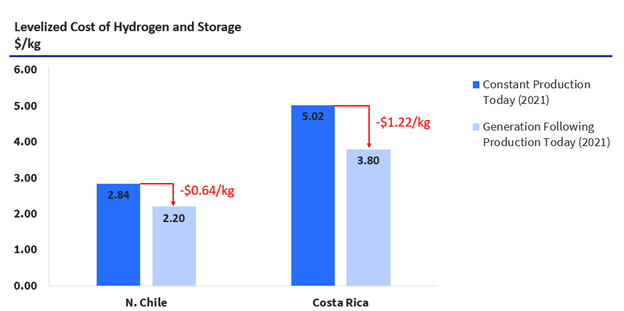
Partial Offtake to Incentivize Green Hydrogen
Utilizing existing grey hydrogen demand as an opportunity to build up green hydrogen capacity could provide an additional pathway for market integration. Partially integrating green hydrogen into current grey hydrogen usage such as in fertilizer production eases the challenge of transition as off-takers are already positioned to use hydrogen in their processes: all that needs to be built is the electrolysis and necessary renewables capacity.
This minimal complexity of green hydrogen adoption will help foster initial project development, leading to electrolyzer capex reduction from economies of scale. Over time as electrolyzer capital costs fall, more and more green hydrogen capacity can be built out at a lower cost, naturally enabling a transition from grey hydrogen use into green while maximizing low-cost installations. As seen recently in India’s mandate for green hydrogen’s integration into existing refineries and fertilizer manufacturing, countries are starting to recognize partial off-take deployment as a method of creating demand and fostering decarbonization today.
Utilizing Curtailed Power to Reduce Costs
Another strategy to foster increased cost competitiveness involves rethinking the mixture of electricity supplied to the electrolyzer. As the electricity input accounts for 50 to 75 percent of the levelized cost of hydrogen today, depending on location, finding opportunities to reduce these costs are critical.
In areas with significant curtailed renewable electricity, such as California or Texas, surplus power is sold at a low or negative prices during times of peak generation. Given the need for abundant and consistent renewables to power electrolyzers today, exclusive reliance on curtailed electricity is likely insufficient to produce hydrogen in an economically viable manner. However, there is opportunity to integrate curtailed power supplemented with complementary, onsite renewable capacity to increase the stability of electricity input. Costs can be saved in reducing the magnitude of new renewables built and the grid can be stabilized through a consistent off-taker of excess electricity.
Accelerating Cost Declines
Green hydrogen is a both a necessary and economically viable pathway for many sectors with limited options for decarbonization. Investors are recognizing this opportunity, and the market is moving. Accelerating the rate at which we grow the gigawatts of green hydrogen installed will quickly foster cost declines and enable us to meet our goals for global decarbonization. The tactics described above can help reduce the costs of green hydrogen production today while capital costs remain high and public policy remains inadequate.
Debates over green hydrogen’s relevance in a clean energy future are no longer meaningful; we know that it is needed. Now is the time to accelerate green hydrogen’s path towards being cost-competitive, sooner than ever expected.