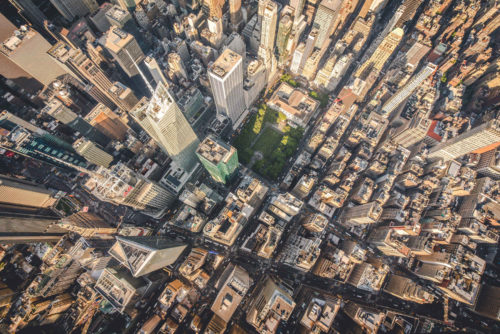
Policy Opportunities to Increase Material Circularity in the Buildings Industry
This policy brief outlines recommended steps municipalities can take to increase material circularity and reduce emissions in the buildings sector.
Urgent action to reduce the greenhouse gas emissions “embodied” in buildings — the emissions associated with building materials and construction or demolition projects — is particularly important to reduce carbon emitted in the next decade, a critical period for climate action. As important as reducing upfront embodied emissions from the extraction, production, and installation of building materials is establishing frameworks to accelerate material circularity, to reduce demand for virgin materials and burdens on landfills. In this resource, RMI outlines policy recommendations that can be implemented by municipalities to increase material circularity in the buildings sector and make progress toward two key objectives:
- Increasing direct reuse of buildings and building materials to reduce demand for newly manufactured products
- Increasing diversion of construction and demolition waste materials from landfills for use as postconsumer recycled content in new building material manufacturing, avoiding extraction and use of virgin materials
Introduction
The overall climate impact of a building is best understood through whole building life-cycle assessment (WBLCA). Life-cycle assessment is organized into stages A, B, and C, which capture upfront, operational, and end of life environmental impacts, sequentially. WBLCA thus includes not only emissions associated with extraction, manufacturing, and installation of building materials (life-cycle stages A1–A5), but also those incurred during the operational (B1–B7) and end-of-life (C1–C5) stages.
Building energy codes and building performance standards rely on advanced energy efficiency and high-performance building systems to reduce emissions from the operational phase of a building’s life cycle (B). Emerging “Buy Clean” policies aim to address embodied emissions for the material production phase (A1–A3) by setting emissions standards, or incentivizing procurement from low-carbon suppliers, for specific materials such as concrete and steel. These policies leave a gap in considering and mitigating the end-of-life climate impacts of building materials.
Exhibit 1: Carbon emissions across the building life cycle
In life-cycle assessment (LCA), the end of a material’s life is the point at which it is removed from its original installed function within a system. In building projects, for example, this can range from de-installation of wood paneling during a tenant improvement project to large-scale demolition of a whole building.
What Happens at the End of Life of a Building Material?
End-of-life climate impacts include greenhouse gas (GHG) emissions associated with deconstruction or demolition (C1), transportation to waste facilities (C2), processing at these facilities (C3), and disposal (C4).
At a high level, there are three scenarios for the disposal (C4) phase for individual building materials:
- Landfilling or combustion of building materials
- Recycling of building materials
- Direct reuse of building materials
A fourth end-of-life scenario applies when whole building systems are preserved, eliminating C1–C4 impacts entirely:
- Direct reuse of the building core and shell (structure, foundation, enclosure)
It is important to note that material reuse, recovery, and recycling that occurs through diversion from a landfill is not typically included within the LCA boundary for the original building or material. It is considered a separate life-cycle stage (D). Take, for instance, the case of a building demolition where structural steel is recycled. Recycling will eliminate the disposal (C4) impacts associated with the material. However, the climate benefits from avoided virgin steel production will be attributed to the production (A1–A3) phase of the subsequent project that uses the recycled steel. Similarly, a new building project that includes direct reuse of an existing building structure or enclosure can take credit for the avoided emissions as part of the production and construction life-cycle phases.
A series of WBLCA case studies presented by World Business Council for Sustainable Development (WBCSD) demonstrated that for new buildings, the estimated end-of-life carbon emissions are small relative to the production and construction (A1–A5) phases. On average, the end-of-life phase in these case studies accounted for less than 2% of the total impacts across life-cycle stages A to C. However, the potential benefits associated with material recovery (stage D) offer a carbon benefit equivalent to 25% of the total A–C life-cycle phases. This demonstrates that the true impact and value of building material recovery and reuse may be underestimated in standard, linear WBLCA methodologies. For many materials, the upstream value to manufacturing processes is more significant than the avoided downstream impacts in landfills. In addition, although estimating future end-of-life scenarios for newly constructed buildings provides useful data points for understanding relative impacts, it does not capture the economy-wide climate impacts of building demolition, given the vast existing building stock.
Current State of C&D Waste Management in the United States
A 2015 study by the US Environmental Protection Agency (EPA) provides some insight into the scale of debris generation and landfill diversion from construction and demolition (C&D) in the US buildings industry. In that year, the industry generated 94 million tons of C&D debris. This total included major building material categories such as concrete, steel, gypsum board, and wood, but it did not include materials such as carpet, insulation, acoustic ceiling tile, or other interior finish materials.
Of this total, 44% of materials (by weight) was landfilled and 39% was crushed concrete waste that found use in recycled concrete aggregate (RCA).
The diversion of concrete from landfills for repurposing as RCA provides meaningful environmental benefits by reducing space needs in landfills and extraction impacts for natural aggregate materials. However, use of these materials may provide only marginal benefits in reducing the global warming potential (GWP) of a concrete mix because Portland cement production, not aggregate sourcing, is the major driver of concrete emissions. In certain instances, mixes using RCA may require additional cement to meet strength criteria, limiting their application for building materials to low-strength mixes. There are emerging research efforts aimed at using recycled concrete in the manufacturing of Portland cement. This application could have a meaningful impact on concrete manufacturing emissions by reducing the need for processing virgin materials into Portland cement.
The 2015 EPA study found marginal material recovery for non-concrete materials, which accounted for only 17% of diverted construction and demolition waste. Recovered wood was used as fuel for energy or heating, recovered gypsum was used as a soil amendment, and recovered concrete, metals, and asphalt found uses in manufactured materials. Metals in particular have high recycling rates due to the high market value of recovered materials. Overall, however, recycling of building materials into manufactured products accounted for only 8%, or 14 million tons, of the 94 million tons of C&D debris in 2015. More can be done to increase the volume of materials that are diverted from landfills to the highest-carbon value next use — manufactured products. Exhibit 2 below illustrates the discrepancy between the total diverted waste for each building material and the diverted waste reused in new products. Both the public and private sector should strive to close this gap.
Exhibit 2: US C&D debris diverted to landfills compared with recycled materials, 2015
Objective 1: Incentivizing Direct Reuse of Building Structures and Materials
Directly reusing structure and envelope components to serve new functions is the most carbon-efficient end-of-life scenario for a building. Renovation of existing buildings not only minimizes demolition, transportation, and disposal impacts, but also prevents emissions associated with new builds. Avoided emissions resulting from building reuse are allocated to the new project and evaluated against a counterfactual condition in which the project was built new. Jurisdictions should consider policy opportunities to accelerate this type of embodied carbon mitigation strategy, allowing developers to achieve the functional needs of new projects while repurposing existing structures.
Historic preservation tax credits have provided financial incentives to revitalize historic buildings for many years. In addition, a number of cities offer incentive programs for adaptive reuse that apply to a wider range of existing buildings. Phoenix provides fee incentives to small businesses renovating existing buildings, while the California cities of Long Beach and Santa Ana provide alternative building standards for adaptive reuse projects. However, these programs are typically designed to support small businesses, improve buildings in specific geographic areas, or allow for common-sense building and fire code flexibility in historic buildings. Broad-based programs specifically designed around mitigating embodied emissions should be considered.
Policy recommendation 1: Planning permit incentive for building reuse
The planning permit submission is an appropriate time for cities to provide value to project teams for renovating existing structures. Jurisdictions should consider providing a standardized incentive program for adaptive reuse projects that demonstrate avoided carbon emissions. The incentive could take the form of fee reductions, density bonuses, parking requirement adjustments, or zoned land use flexibility benefits as part of the planning permit process for adaptive reuse projects. Incentives can be tiered and sized commensurate to the embodied carbon emissions avoided through building reuse.
Project teams can demonstrate performance to achieve a planning permit incentive through one of the following approaches:
- Path 1: US Green Building Council LEED building reuse credit language
- Maintain 75% of the existing building structure (including floor and roof decking) and envelope (the exterior skin and framing, excluding window assemblies and nonstructural roofing materials)
- Path 2: Whole building life-cycle assessment (WBLCA)
- Conduct a life-cycle assessment of the project’s structure and enclosure, evaluated against an equivalent, newly constructed baseline project. Demonstrate emissions reductions in excess of 50%
Policy recommendation 2: Prescriptive new construction design standards to enable future adaptability
While decisions around building reuse will have been made prior to the building permit submission, green building code standards are an appropriate place for establishing criteria for designing new building projects for future adaptability. Jurisdictions can provide specific guidance for project teams to demonstrate that the building or structure has been designed to accommodate functional transformation in the future or that it has been designed to facilitate disassembly of individual materials for source separation.
Jurisdictions can include prescriptive standards or guidelines in green building code to enable future adaptability of spaces, targeting newly constructed parking structures and large commercial buildings exceeding 100,000 square feet (sf). The following suggested strategies can be included in these guidelines:
- Clear spans create wide-open spaces full of possibility, allowing for multiple alternate uses of the interior in the future without costly structural alterations.
- Flat floors with few transitions from one floor height to another enhance versatility.
- Interior non-load-bearing partitions instead of load-bearing walls help ensure that programs can be adapted without threatening the structural integrity of the building.
- Regularly spaced structural elements where clear spans are not feasible allow for simpler, more flexible planning when adaptation takes place later in the building’s life.
- Separation of systems from one another and from the envelope of the building helps ensure that the building’s mechanical, electrical, plumbing, IT, and other services can be maintained, replaced, or upgraded without damage to the building or to other services.
- Design for disassembly practices, such as modular design of interior partitions and use of screws rather than glues or nails for connection points, will simplify material recovery and conversion of space.
More information can be found in the AIA Design for Adaptability, Deconstruction, and Reuse guide.
Objective 2: Increasing Diversion of Building Material Waste from Landfills
Policy recommendation 3: Improved construction and demolition waste management ordinances
In many jurisdictions, C&D waste management requirements are imposed on builders as part of the building permitting process. For example, the California Green Building Code requires diversion of 65% of construction and demolition waste from landfills. Builders demonstrate compliance through the submission of a waste management plan document, through the use of a registered waste management company, or by meeting a total disposal waste reduction target (<2 lbs/sf for nonresidential and <3.4 lbs/sf for residential new construction). C&D waste management ordinances are a key first step to build capacity among waste management facilities for diverting building material waste streams.
There are a few ways to improve these policies to increase source-separated waste diversion, which can streamline recycling of building materials. Jurisdictions can provide incentives (administrative or financial) for source separation of building waste materials in construction waste management ordinances, targeting high-volume, high-impact materials such as metals, concrete, wood, gypsum board, insulation, and float glass. An example of this approach can be seen in San Francisco, where all transporters and processing facilities for mixed C&D debris must be registered and permitted by the Department of the Environment, while companies hauling source-separated materials are exempt from such requirements.
Policy recommendation 4: Deconstruction ordinances
To increase recovery and reuse of high-quality building materials, especially from historic buildings, jurisdictions can establish ordinances that require deconstruction rather than demolition. Deconstruction ordinances catalyze local material recovery markets, reducing demand for virgin materials and creating jobs in skilled deconstruction. The City of Portland (Oregon) Deconstruction Ordinance, the first of its kind in the United States, applies to demolition permit applications for primary dwelling structures built in 1940 or earlier or those that have been designated a historic resource. Deconstruction must be completed by a certified deconstruction contractor. Deconstruction ordinances improve direct reuse of lumber materials, such as framing and flooring, which lose value once they are destroyed through conventional demolition practices.
Jurisdictions with a significant stock of small and/or historic buildings vulnerable to demolition can adopt deconstruction codes for structures built before 1940 and with less than 10,000 square feet of occupied area. Enforcement would occur when projects seek demolition permits. Jurisdictions should conduct outreach and provide workforce training opportunities to develop a robust market for certified deconstruction contractors. Exemptions can be granted for structures that are structurally unsafe, do not have reusable materials, or are unsafe to deconstruct.
Policy recommendation 5: Material passports
The material passport is an emerging concept for increasing the potential for material recovery in newly constructed building projects. A material passport for a building would provide detailed information about the construction materials and assemblies, demonstrating the embedded value of these materials for future recovery. Material passports can not only document material composition and potential for recyclability, but also describe how components are assembled to facilitate deconstruction at the end-of-life phase. In addition, material passports can be used to document the embodied carbon of installed building materials, summarizing the long-term carbon value of the products. Consistent standards for material passports have not been developed; Madaster is a platform piloting this concept and aims to scale the strategy in mainland Europe.
Jurisdictions can establish material passport pilots for new construction projects for public buildings, increasing documentation of building material properties up front to facilitate future material recovery. Project teams can leverage design phase whole building life-cycle assessment (WBLCA) processes to create material passports that can be referenced during the building occupancy, maintenance, and end-of-life phases. Elements of such a plan could include:
- Requiring WBLCA by design teams for new construction and interior scope of work exceeding 10,000 square feet
- Leveraging WBLCA and building information modeling to develop standardized documentation practices for material passports
- Targeting documentation of high-volume interior fit-out materials:
- Carpet
- Gypsum board
- Interior partitions
- Extruded aluminum
- Cold-formed/extruded steel channels
- Interior insulation
- Acoustic ceiling tile
- Key data reporting requirements to promote disassembly and reuse:
- Disassembly process
- Material and product composition
- Physical properties (dimensions, weight, service life)
- Source mill
- Weldability (for metals)
- Production date
- Usage history
- Product ownership (product leasing, take-back guarantees, recycling system logistics)
- Reuse potential and recyclability
- Second-life options for direct reuse