RMI collaborated with the China Automotive Technology and Research Center (hereinafter referred to as “CATARC”) to launch a nine-month pilot project calculating the carbon footprints of steel products used by four major automotive manufacturers in China. The pilot utilized the methodology introduced by RMI's Steel GHG Emissions Reporting Guidance (hereafter “Steel Guidance”). Eight companies participated, including the steel enterprises Baosteel, Angang, HBIS, and Baotou Steel, which account for ~12% of the world's steel supply. Four automobile enterprises, Volvo, NIO, Dongfeng Nissan, and one unnamed manufacturer also participated as downstream buyers and data receivers. RMI developed an Excel calculation tool for steel products based on the Steel Guidance, and CATARC provided a data platform that could realize data transfer and prove the transparency and comparability of steel products’ carbon footprints along the auto supply chain, supporting downstream car companies in making low-carbon procurement decisions. These types of procurement decisions will become increasingly important for automotive companies as the switch to electric vehicles will bring an increased need to reduce their upstream supply chain emissions.
Case Study
Steel:
CATARC – Baosteel – Angang – HBIS - Baotou Steel
RMI collaborated with the China Automotive Technology and Research Center (CATARC), Baosteel, Angang, HBIS, and Baotou Steel to pilot steel product-level greenhouse gas (GHG) data reporting following RMI's Steel GHG Emissions Reporting Guidance (hereafter “Steel Guidance”).
At A Glance
" Both automotive and steel companies in the pilot believe that enhancing mutual recognition of carbon accounting methodologies between upstream and downstream, as well as domestically and internationally, will help reduce the cost and complexity of corporate carbon disclosures and accelerate decarbonization across the supply chain. "
Targeting Industry Challenges
China is the world's leading automotive manufacturer, and the industry plays a crucial role in the Chinese economy. In recent years, China's automotive industry has led the world in electrification and is now the world's largest producer of electric vehicles. Although EVs produce zero tailpipe emissions, achieving full lifecycle emissions reductions in the automotive industry requires decarbonization and reduction of embodied carbon in vehicle materials, of which steel is the largest contributor.
China still faces prominent challenges in achieving net-zero emissions vehicles. Upstream steel producers and auto-manufacturers lack a consensus on how to collaborate for industry-wide decarbonization. There is a need to establish product-level carbon accounting methods, improve emissions data quality and transfer, and management capabilities of raw material suppliers. There is also a need to reach consensus around key concepts such as by-product calculations and the definition of “low carbon emission steel.” Steel is one of the most emissions-intensive materials used in automotives, accounting for 50% of the weight of a passenger car and 33% of its carbon embodied emissions, according to the China Automotive Technology and Research Center. making it a material that car companies should first consider for low-emissions procurement. Enabling procurement of low-emissions steel by Chinese automotive companies will require addressing the above challenges, having in-depth discussions on product-level carbon accounting methods, and reaching a consensus to achieve comparability of the calculation results.
Our Objectives
In this pilot, RMI's Guidance was used to:
Test a carbon accounting methodology for steel products that supports low-carbon purchasing decisions – RMI developed best practices for carbon accounting for steel products, introducing key features such as a benchmarking emissions boundary, introducing calculations of scrap ratio, encouraging primary data sharing, and linking emissions reduction impact with different production technologies to effectively reflect companies’ carbon reduction efforts and to provide a comparable basis for automotive companies to purchase low-carbon emission steel.
Socialize a standardized data format and data platform – The Steel Guidance adopts and extends the data format compatible with the WBCSD’s PACT Pathfinder Framework, promoting international alignment of standardized emissions data exchange. The data platform used in the pilot is China Industrial Carbon Emission Information System (CICES), a data transfer platform specifically for automotive companies and their suppliers in China. During the pilot test, the PACT-aligned steel data extension is incorporated into the CICES platform for data transfer and to increase efficiency and comparability.
Enhance collaboration on emissions reporting and data exchange across the automotive value chain - RMI and CATARC held workshops and seminars to discuss the accounting methods and key indicators of the Steel Guidance with more than 40 experts from the steel-automobile industry supply chain and conducted carbon accounting and data transfer pilot tests for automotive steel products with four steel companies and four car companies.
Pilot enabled changes
- Insufficient primary data collection, mostly using default emission factors
- Data collection at the site-level, lacking product-level data
- Encourage the collection of primary activity data
- Introduce the “primary data share” indicator as a reference for data quality
- Auto manufactures obtain data from suppliers one by one
- Lack of a unified data format results in inconsistent data provided by different suppliers
- The carbon emission data can support companies in setting and reviewing their Scope 3 emission targets and understanding suppliers' carbon footprint
- Key metrics provide extra information on steel products, ensuring the procurement of low-carbon emission steel and supporting decarbonization
Highlights
For the first time in China, emissions data under a standardized data format was transferred digitally, promoting compliance with international data standards. The digital platform used in this pilot, CICES, is the first integrated data collection and transfer platform for the industrial sector within China. The collected data involves 18 vehicle manufacturers (17 passenger car companies and 1 commercial vehicle company), more than 24,300 supply chain companies, and over 300,000 automotive products (as of June 30, 2024), creating a set of interactive standardized forms widely used in the Chinese automobile industry. In this pilot, CICES integrated the unified data format from the Pathfinder Framework and additional key metrics from the Steel Guidance, ensuring that steel companies disclose standardized data to automotive companies. This facilitates an intuitive and standardized comparison of product carbon footprints from different steel companies by car companies.
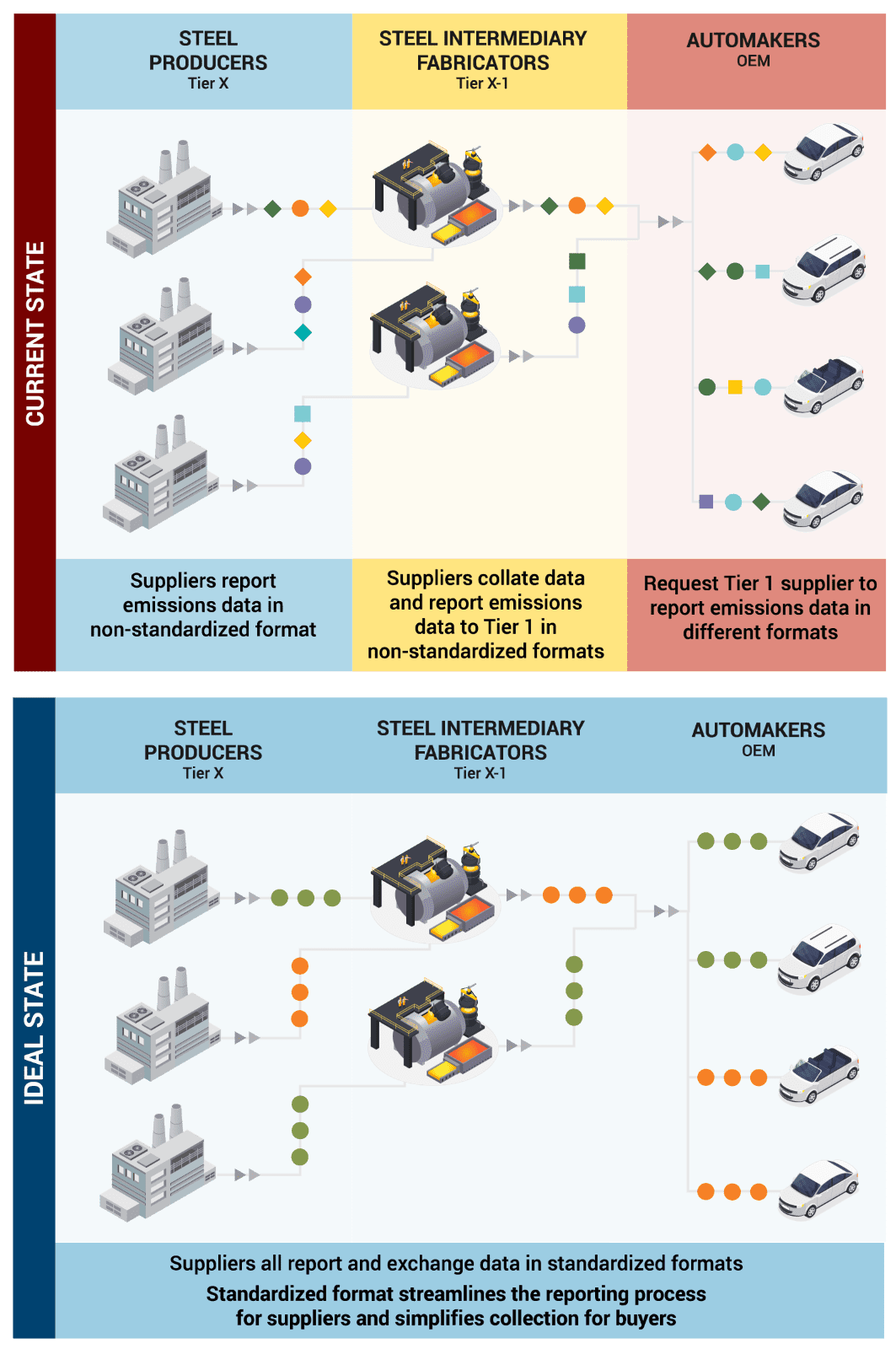
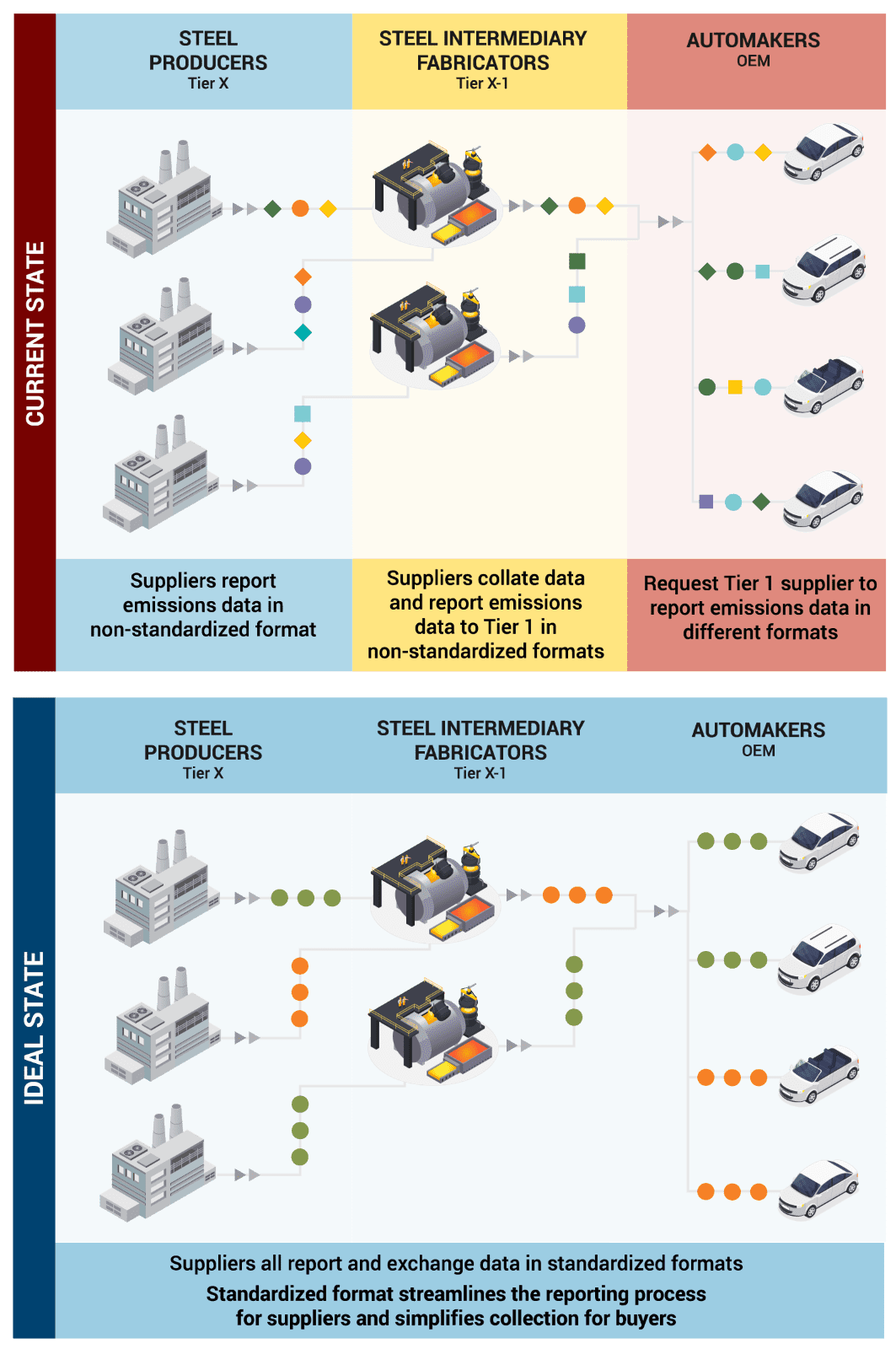
The pilot test enhanced the construction of a data platform within the automotive supply chain. The pilot test improves the digital aspect of data collection, transfer, and analysis, which is crucial for monitoring and managing carbon footprint along the entire automotive supply chain. The results of the pilot contribute to enhanced data transparency and interoperability within the industry, better enabling companies to achieve their long-term decarbonization goals.
Pilot participants believe that the “fixed benchmarking boundary” enhances the comparability of different steel products. Compared to the cradle-to-gate accounting boundary, the “fixed benchmarking boundary” concept proposed in the Steel Guidance enables the carbon footprints of different steel products to be comparable. The benchmarking boundary involves emissions from cradle to hot rolling (or crude steel as an alternative proxy point), which includes all the emissions-intensive processes during steel production and is aligned with international steel accounting methods. Automotive companies participating in the test believe that the benchmarking boundary helps compare the carbon emission intensity of different steel products, supporting their low-carbon procurement.
The disclosure of key metrics provides quantitative references for automotive companies to procure low-carbon emission steel. The “primary data sharing,” “scrap rate,” “technology label,” and “benchmarking boundary emissions” recommended by the Steel Guidance help automotive companies comprehensively understand the quality of steel carbon accounting data, and the decarbonization technologies and different level of investment by steel companies, and assess the emission reduction efforts of steel companies. This enhances the transparency of product climate metrics and supports low-carbon procurement decisions.
Pilot companies recognize the importance of international alignment on carbon accounting methods within the steel-automobile supply chain. Both automotive and steel companies in the pilot believe that enhancing mutual recognition of carbon accounting methodologies between upstream and downstream, as well as domestically and internationally, will help reduce the cost and complexity of corporate carbon disclosures and accelerate decarbonization across the supply chain. Third-party organizations like RMI and CATARC could leverage their strengths in technical support and data platforms to assist in the integration of industry carbon accounting systems.
Remaining Challenges
RMI's Steel Guidance solves some of the barriers to the procurement of low-carbon steel in the automotive sector. However, certain challenges remain:
1. Further exploration is needed to determine how to apply the key metrics to low-carbon procurement decisions. The key metrics provided by the pilot can help automotive companies obtain suppliers' product-level emissions information and select low-emissions products. However, most automotive companies have not yet effectively integrated this information into procurement decisions and cross-department collaborations to realize their decarbonization goals. It is necessary to continuously improve the transparency of carbon emission information and accounting capabilities of raw material suppliers through supply chain management.
2. Future efforts are required to focus on standardizing and mutually recognizing the data disclosure format for product carbon footprints across industries. Currently, there is a lack of a unified data format for disclosing product carbon footprint data in China. This pilot also used an Excel-based data reporting mode, which requires learning investments for reporting companies. In the future, efforts should be made to enhance the digitization of product carbon footprint data disclosure based on existing platforms, reduce additional labor and learning costs, and strengthen standardized data disclosure processes.
The Path Forward
Strengthen research and capacity building for the application of carbon accounting results to promote supply chain cooperation in decarbonization: In the future, the project team will continue to assist on knowledge sharing and capacity building to improve automotive companies' comprehensive evaluation and comparative analysis of carbon accounting results, supporting them in developing supply chain emission reduction strategies based on these results and further promoting collaborative carbon emission reduction between supply and demand sides.
Support automotive companies in integrating key metrics into steel procurement decisions and foster a low-carbon emissions steel market: Leading automotive companies around the world have already started procuring low-carbon emissions steel by signing long-term procurement contracts with steel companies and investing in low-emission production projects. Future projects will further explore how to support automotive companies in integrating low-carbon metrics into steel procurement decisions and support upstream-downstream dialogues to enhance the influence of downstream companies in incentivizing upstream raw material decarbonization, contributing to the formation of a low-carbon emission steel market.